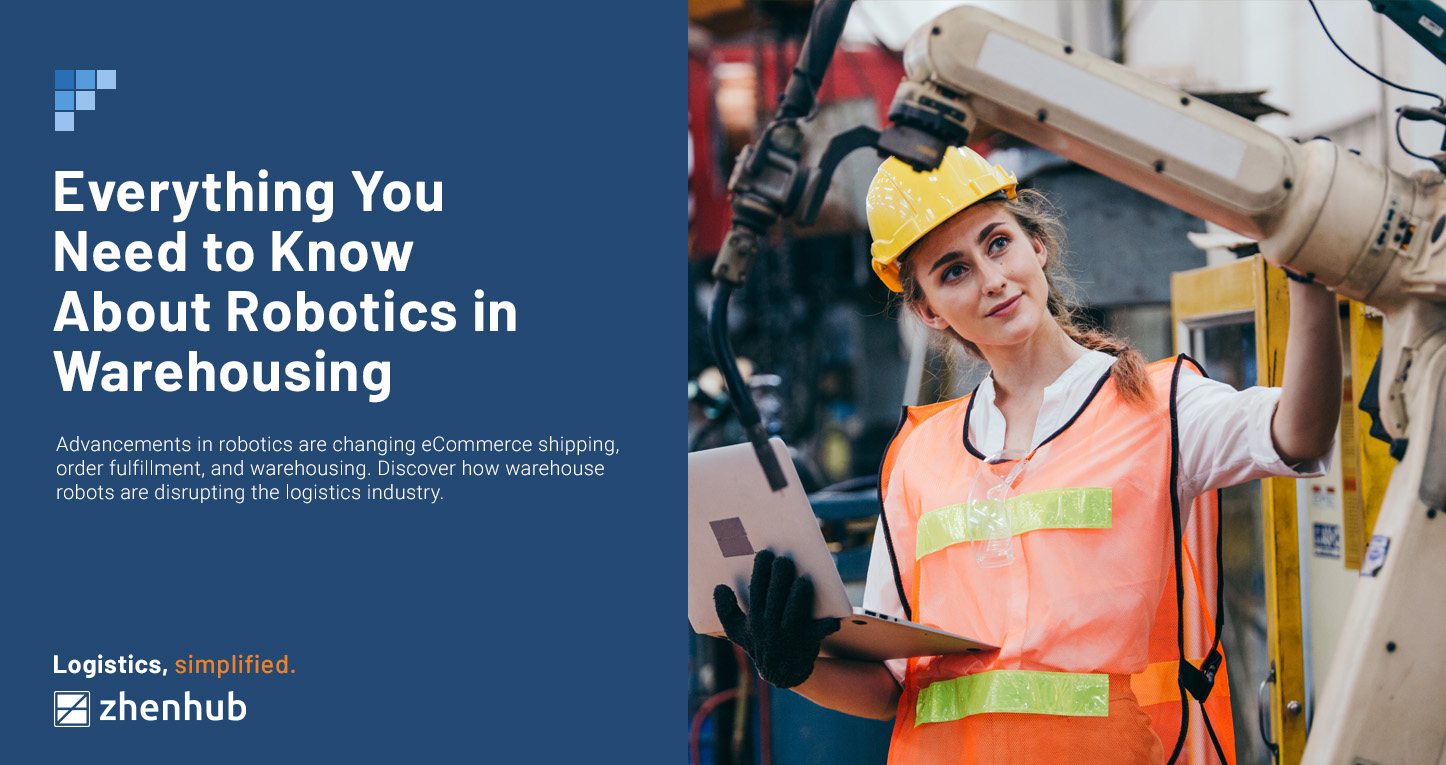
Everything You Need to Know About Robotics in Warehousing
Time to read: 5 minutes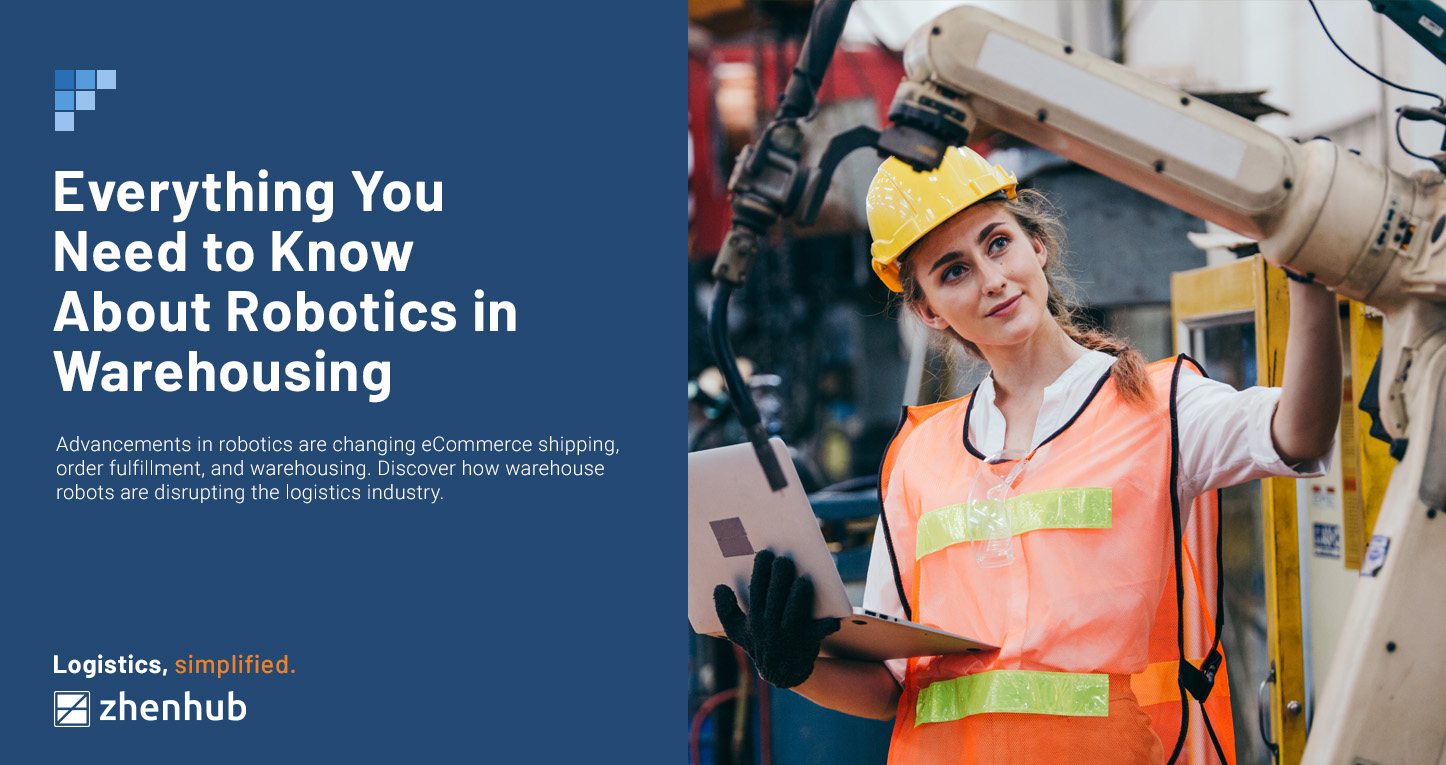
The technology powering warehouses is becoming quicker, more robust,, and smarter. Advancements like barcode scanners, direct fulfillment centers, and warehouse management systems have significantly increased the productivity of warehouse personnel.
Global retail and logistics are undergoing radical changes due to eCommerce growth. To keep up with global supply chain issues, more firms are starting to see the advantage of robotics in warehousing.
Logistics automation has recently become a significant priority for many online retailers. It’s a direct response to a growing need to handle larger volumes of online orders daily. Businesses will need to keep up as the online sales of physical goods are projected to surpass $563.3 million by 2024.
Conveyor belts, scanners, and other technological advancements have long helped to automate and accelerate the logistics industry. Speed is a necessity making robotics and automation essential.
But the pandemic-era eCommerce boom, a competitive labor market, and a precarious supply chain have accelerated investments into automation. According to experts, robotics will alter the operation and layout of warehouses.
Getting Started With Robotics in Warehousing
Robotics in warehousing is an autonomous machine created to supplement or replace human labor in a manufacturing or logistics setting. In this sense, a robot is a two-part system consisting of the machine designed to do a specific task and the software that directs it.
Robots are often one-purpose devices. Some move materials from one warehouse slot to another or the loading dock. Other robots can reorganize the warehouse by shifting entire racks to make a more efficient area.
Companies can also integrate robots into warehouse management systems with more advanced sensors and powerful processing capabilities. The contribution of robots to supply chain automation is so great that their market value could grow to $27 billion by 2025, That’s more than double its value of $13 billion in 201.8
According to polls conducted by the Material Handling Institute, an industry trade association, the adoption of robots in warehouses will rise by more than 50%over the next five years. The objective is mechanical orchestration. It’s Where a group of robots can move boxes and items in a seamless environment controlled by advanced software and artificial intelligence.
Warehouses are replete with repeatable, process-oriented, and error-prone procedures. Robotics and automation can replace people in repetitive tasks like picking, receiving, and storage. It can help improve consistency, accuracy, and productivity in daily warehouse operations.
Relieving workers of tedious and repetitive activities can increase employee engagement and retention rates. Workers can take on additional responsibilities including customer service, upkeep, and operational analysis. Automation and robotics in warehousing also makes it safer as people won’t work around dangerous machinery, heavy equipment, and other working situations.
Practical Examples of Robotics in Warehousing
The next generation of robotics in warehousing is designed to support workers and work together. Industrial robots have been around for a long time. But their capabilities were frequently constrained and often cordoned off to protect workers and equipment. New warehouse robots employ AI to move about a space, collect products, and plan interactions with humans.
1. Robot Arms
Companies have used robotic arms in production for years and in case distribution settings. Better performance for piece picking and pick and place operations are now possible with vision systems and end effector (gripper) technology developments. These arms can be mounted to a mobile robot or utilized at a goods-to-person (GTP) workstation for picking tasks. They can also be permanently placed to handle repeated activities, including putting empty boxes into an overhead conveyor. It can also add discrete units to a unit load sorter and organize it into shipping lanes for outgoing shipments.
Robotics in warehousing can reduce workforce requirements at pick stations, put walls, unit sorter induction stations, and the shipping dock. Pick and put processing accuracy is also greatly improved.
2. Automated Guided Vehicles (AGVs)
Automated guided vehicles are robots that move supplies and inventory across a warehouse. It can move goods from one department to another or from a picked goods section to a packaging room. The robot may move its cargo in a specific way or may have other functions depending on the model. For instance, some types can pull a trailer or pick up and transport pallets, while others can carry a load. Some can even transport goods from heights using built-in forklifts.
AGVs can take the role of forklifts and pick carts by traversing the warehouse with the help of integrated markers or sophisticated LiDAR. This technique enables robotics in warehousing to collect data from reflections from a rotating laser array.
3. Autonomous Mobile Robots (AMRs)
Intelligent robots called autonomous mobile robots can independently navigate constantly changing warehouse conditions. They don’t require additional supervision, unlike AGVs. , it uses various visual, audible, thermal, touch-based sensors, onboard computers, and maps. As a result, AMRs can observe their environment and plan routes, even change them in the event of any roadblocks.
AMRs are versatile robots in warehousing that can perform a variety of activities. They may travel in front of or behind pickers to the next stop on their path. It makes them ideal for moving stock throughout the warehouse and delivering products to pickers and packers. AMRs have sophisticated sensors that can recognize and interpret information on item packaging, enabling putaway, sorting, and inventory check operations.
Some notable examples of AMRs currently being used are mobile rack systems, which help transport products contained in various storage unit configurations. Roaming shuttle AMRs can also store and transport products in a high-density storage/retrieval environment.
4. Collaborative Bots (Co-Bots)
Among the newest category of robots, cobots or co-robots are ones that interact with people in a collaborative workspace.
Cobots fall between fully autonomous and under human direction. Many of them have been designed to follow workers as they choose different orders while they move about. Others can operate autonomously in environments where people are also employed; thanks to their sophisticated sensors, there is minimal chance of a collision.
The main benefit of co-bots is their capacity to minimize the trip time of pickers who collaborate with them. Pickers spend most of their time walking, and these bots cut down on some of the time spent on transportation.
Upgrading Your Processes with Robotics in Warehousing
As part of a warehouse automation strategy, you may enhance facility operations and start making use of what robotics in warehousing can provide.
Nevertheless, acquiring and implementing these technologies in your warehouse is not straightforward. You must have the proper system \ to support any robots so they may operate optimally. Investing in a reliable warehouse control system that enables seamless connection is essential.
Every business can employ robotics in warehousing, but some adopt them more quickly than others. As mentioned previously, robots are being used increasingly in online shopping. Amazon, for instance, used over 200,000 robots in its warehouses as of 2019, and other eCommerce leaders quickly followed suit. TechCrunch and Walmart began using autonomous robots in 25 distribution sites last year.
Although robotics in warehousing may seem like a costly investment, they can carry out a variety of jobs there without the risk of getting tired or injured. These technologies give businesses a competitive edge by eliminating risky and repetitive jobs while boosting production, efficiency, and income.
Businesses may automate additional procedures and create new efficiencies throughout their warehouse by connecting robots with top supply chain management systems. A company may be able to refresh its inventory using robots instead of manually monitoring stock levels. Reversing the usual workflow and bringing items to the employees can enhance warehouse productivity.
Robotics in warehousing, when implemented correctly, can pay for themselves once your organization reaches scale and you have the appropriate infrastructure in place.
Robotic warehouses have advanced significantly. Initially, warehouse robots could only execute the most basic, pre-planned movements since they’re bolted onto the floor. Modern warehouse robots eventually achieved autonomy as well as more freedom of movement. Warehouse management software and robotics currently collaborate to support human effort and planning abilities. But to make a warehouse safer, quicker, and more efficient will still require the decision-making and input of hard-working human staff.
ZhenHub helps your online business overcome logistical hurdles with modern warehousing and fulfillment solutions. With trackable shipping services and a distribution network of global warehousing partners, you can be in a prime position to integrate robots into your logistics strategy. Sign up now and revolutionize your eCommerce business.